Health care workers across this country rely on personal protective equipment such as medical masks and face shields to protect themselves and their patients from being infected by COVID-19.
However, the growing demand for such personal protective equipment amid the coronavirus pandemic has caused prices to surge and supplies can take months to be delivered.
While many medical centers across the country are running extremely short on protective gear such as surgical masks, Augusta University Health has been fortunate with the level of its supplies at this time.
But a number of faculty members from Augusta University have teamed up with local companies such as Solvay Specialty Polymers, Club Car, Textron, software engineer David Stevens from the Savannah River Site and MTU Solutions to produce 3D-printed molds and create at least 500 reusable face masks for AU Health to make sure members of its clinical staff always have the protective equipment they need to combat COVID-19.
The making of the Montana Behr Mask
Lynsey Ekema, a board certified medical illustrator for the Center for Instructional Innovation at Augusta University, has led the effort to pull together a task force that has provided AU Health with 1,000 3D printed face shields and the group is also in the process of making 500 face masks molded from silicone.
These reusable silicone masks have been nicknamed the “Montana Behr Mask.”
The initial idea of reusable face masks came from the Montana Mask, which is a plastic filtration face mask designed for 3D printers by a college graduate and two medical professionals in Montana.
The Montana Mask’s design files are free and available for the public’s use, Ekema explained.
The task force at Augusta University wanted to develop a similar face mask that could be sanitized and reused, but would also be more comfortable for the clinical staff to wear.
“We called it the Montana Behr Mask, because Amanda Behr is faculty in the medical illustration department and also an anaplastologist at The Dental College of Georgia’s Anaplastology Clinic at Augusta University. She took the open source platform provided for the Montana Mask and edited the design to develop a prototype that would meet the approval of our medical center, but also be more comfortable for our staff,” Ekema said, adding that the Montana Behr masks are created using silicone because it’s a much lighter, comfortable material.
“This is the same material that is used in prosthetics with the DCG Anaplastology Clinic and Amanda Behr here at Augusta University has been absolutely incredible. She has been right there with us through this whole process, showing the entire team how to make these masks using the 3D-printed molds.”
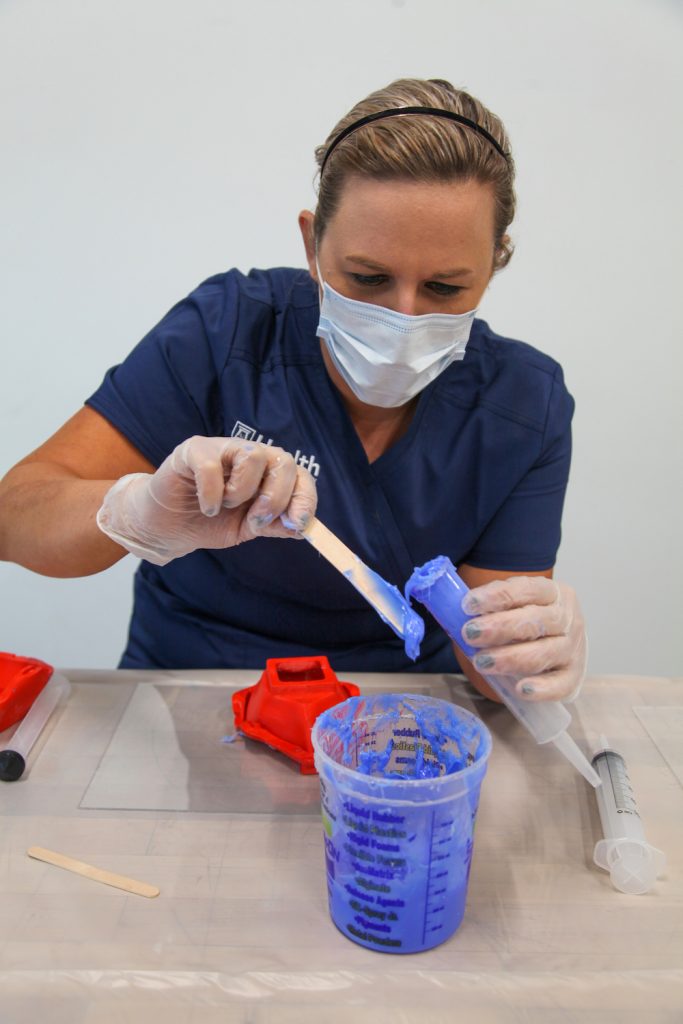
The DCG Anaplastology Clinic at Augusta University provides patients with custom-designed, non-weight bearing prostheses to individuals living with anatomical anomalies, such as congenital absence of a body part, amputation from trauma or loss from illness.
Behr regularly designs prosthetics such as ears, eyes and noses for her patients, so she volunteered to use that expertise during this pandemic to develop much more comfortable masks made of silicone that could be easily sterilized and reused by the clinical staff at AU Health.
“By these being reusable, employees at the hospital can disinfect them with an alcohol swab and change up the filters, so they can hold onto these masks and reuse them,” Behr said. “And, because of the material that they’re made of, as long as employees at the hospital take the straps off of the masks, they can be sterilized when they need to be.”
Solvay joins team to help protect AU Health staff
When Alain De Greef, the site manager at Solvay Specialty Polymers, heard about the development of the 3D face shields and masks by the task force at Augusta University, he immediately wanted to see if the company could help.
“A few weeks ago, a colleague here at Solvay named Michael Ray came and told me about the project to develop silicone masks at Augusta University because his wife is a nurse at the hospital,” De Greef said. “While we are not in the silicone business, I knew a little bit about it and I said, ‘I don’t know if we can help, but at least we will try.’”
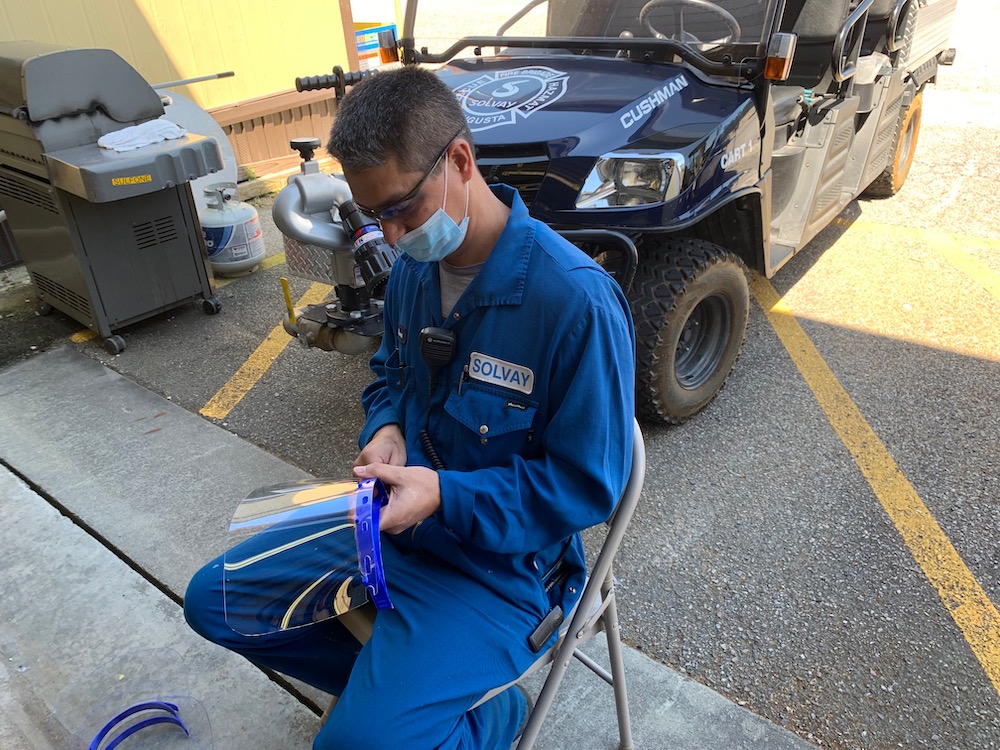
Solvay staff began by reaching out to some of their connections in both South Carolina and Georgia to find individuals willing to assist in developing the molds for the masks using 3D printers.
Solvay’s technical manager, Ron Mysona, teamed up with Michael Ray to see if they could provide Augusta University with some of the materials and assistance it needed.
“My wife also works at Augusta University, she’s an assistant research scientist, so we wanted to help,” Mysona said. “Here at Solvay, we have a saying that, ‘We bond people, ideas and elements to reinvent progress.’ We believe in that and we enjoy helping out the community, so I said, ‘Let’s keep going and see if we can find a way to do this.’”
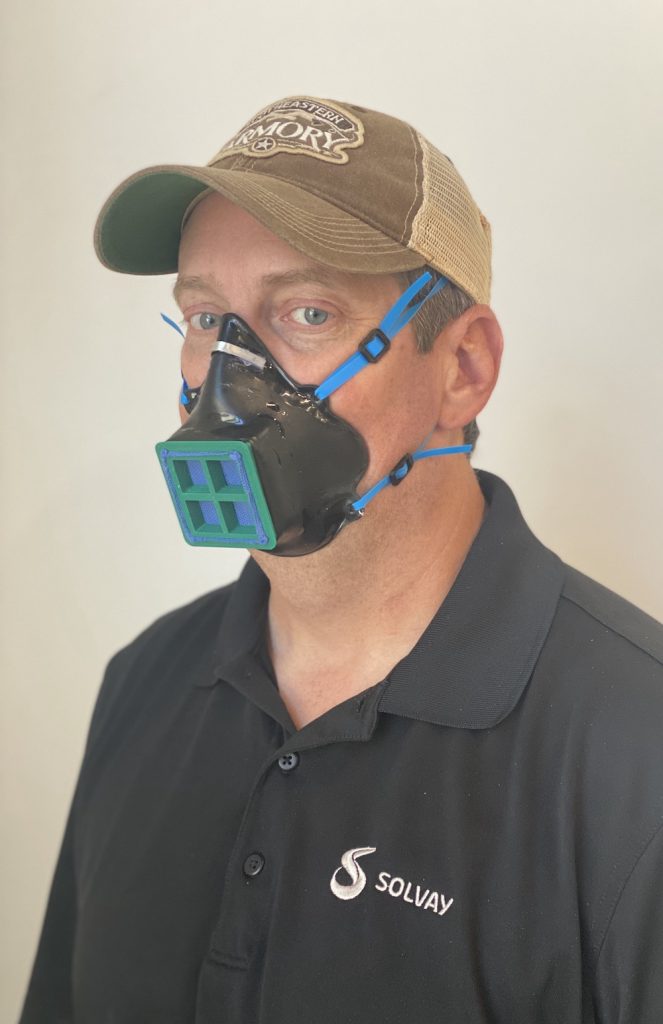
Mysona reached out to both Club Car and Textron and both companies generously volunteered to use some of their 3D printers to make the molds for the Montana Behr masks.
“We have a lot of connections here in the local community, too, in terms of industry, so we started to ask around if any of them had 3D printers,” Mysona said. “Sure enough, we found a couple other industries that were willing to volunteer time on their 3D printers. And so, we started printing molds for Augusta University with those 3D printers as well.”
Since becoming involved in the project a few weeks ago, Solvay has already donated 250 Montana Behr masks with 3D printed molds, 250 face shields and 15,000 disinfectant wipes to Augusta University.
Solvay’s 250 donated masks are being made with AOPI Orthotics and Prosthetics owner Tripp Rice and employees April Everatt, Justin Hansome, Adam Trefethren and Nubia Key.
“This is all due to Michael Ray’s creativity and dedication in trying to creatively problem solve a faster and more economical solution,” Ekema said. “These masks are in production this week.”
The team at Augusta University is also developing ear savers and modified grids for face masks to make them more comfortable for employees at the hospital.
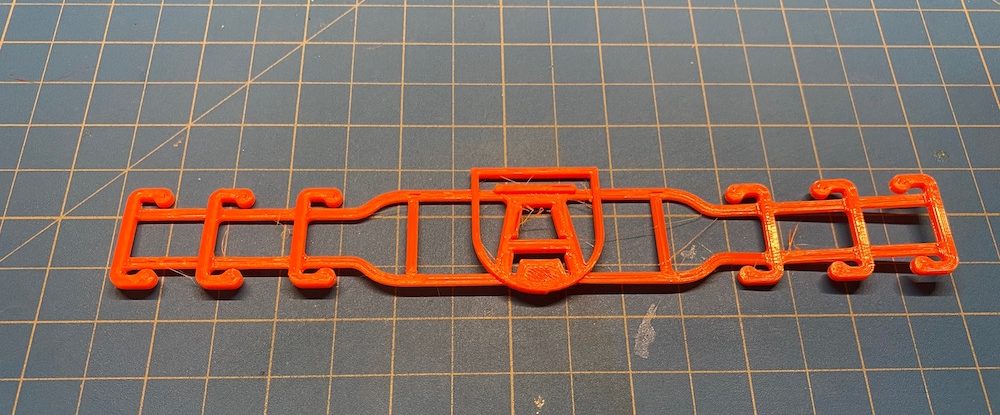
Just last week, Ray and Mysona began volunteering their time to learn how to properly pour the silicone into the molds to develop the Montana Behr masks.
“We want to really help Lynsey and her team reach that goal of 500 of these silicone masks,” Mysona said, adding that they began working with Behr and Ekema along with a group from Augusta University’s Department of Art and Design to develop the masks. “The team over there is obviously being really innovative and we like to see that innovation and that way of thinking.”
The art of molding a Montana Behr mask
Professor Brian Rust, Assistant Professor Marianna Williams and studio technician Brian McGrath from the Department of Art and Design at Augusta University were eager to help develop the Montana Behr masks when they heard about the project.
“It’s been awesome,” Williams said, explaining that she teaches a sculpture class at Augusta University and wanted to bring her expertise to the table. “Everyone on the task force has been working super hard, and both Amanda and Lynsey have been amazing to work with. It has been really interesting to see how we can take that Montana Behr mask and refine the mold to get the inside surface a little smoother, so that it releases properly. We have also learned how to heat the silicone up to make it medical grade.”
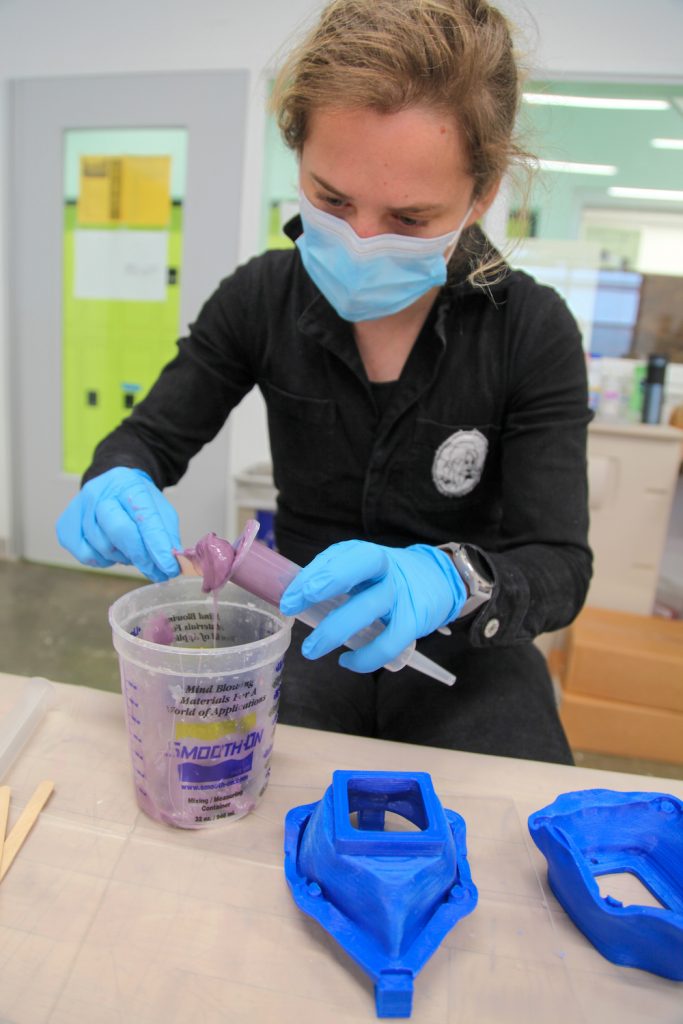
Williams said she learned about the project from Cheryl Goldsleger, the Morris Eminent Scholar in Art at Augusta University, who has spent the past several weeks helping to develop face shields for AU Health.
“It’s kind of interesting to take an issue like this and come up with a creative way of attacking that problem,” Williams said. “There’s just so much overlap between art and medicine, and between art and fabrication, and it’s been really cool that Augusta University has been able to get behind it. This is just a great example of bringing people together and finding solutions.”
Rust, who has worked with a great deal of plaster molds in his artwork over the past 20 years, said learning to develop the Montana Behr masks was fascinating.
“It’s a much different process than say, if I was doing something for a class or for my own work,” Rust said, explaining that for his artwork, he would engineer a mold with the least amount of sharp edges so it would be easier to cast and remove from the mold. “But with this mask project, they have worked very specifically to get this one design of a surgical-equivalent mask that includes a square front. So, when they ended up printing the 3D molds, it’s a pretty complicated form and there are a lot of steps. And, of course, there’s a high standard to make them all uniform.”
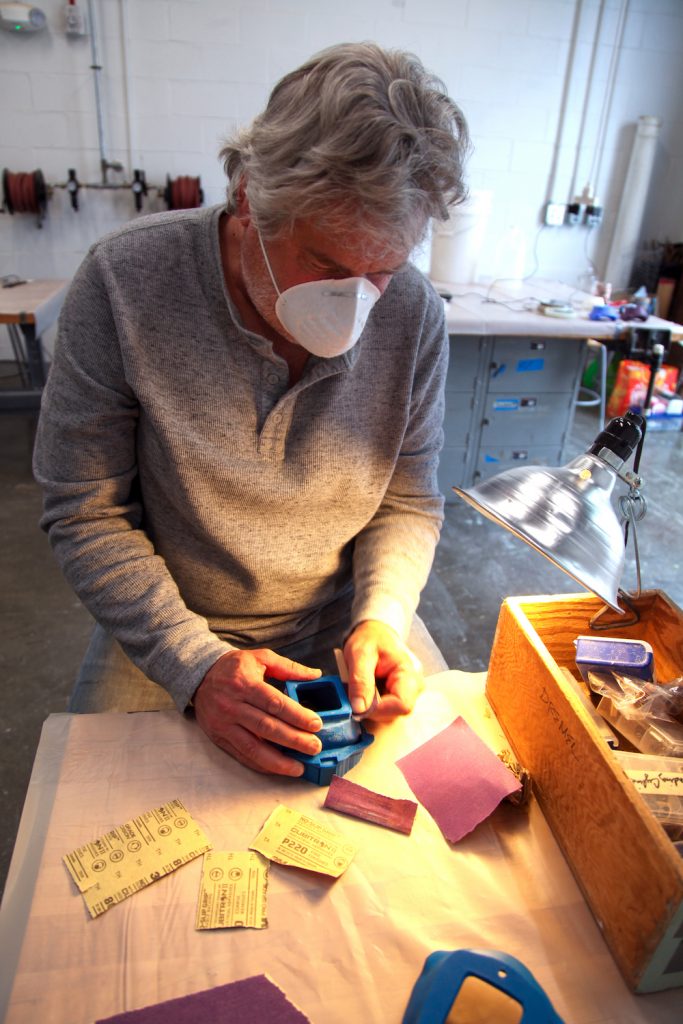
It’s a slow process because the silicone has to be injected into the molds using large syringes, and there can’t be any air bubbles caught in the mold before it is cured, he said.
“This particular silicone is thick, kind of like Vaseline,” Rust said. “And you’re using these large syringes to squirt this thick, jelly substance down into all the areas of the mold. Once the silicone is cured or baked at about 150 degrees for an hour, then it has to sit overnight. So, I mean, it’s a slow process and then it has to be popped out of the mold and properly cleaned up.”
The entire team helping Augusta University accomplish its goals also includes Stephen Campbell, Jonathan Goolsby, Erika Grimm, Bill Gray, Paul York, John Peterson, Dale Strasser, Scott Thorp, Aaron Cummings and Jessica Dinsmore.
Rust said he is thrilled that he’s been able to help create these reusable masks to assist the clinical staff at AU Health.
“These masks were needed and Amanda and Lynsey came up with a way to make them,” Rust said. “It’s funny because that’s how art is. Sometimes you have to make your own tools or the objects you need for art, so I’ve been impressed at how similar our approach is to creating things that we need to get the job done.”
Coming together for front line workers
The team at Solvay said they also want to do whatever they can to help the employees at AU Health.
“I think folks at the hospital are really appreciative of what we’re doing and obviously that energizes us, too,” Mysona said. “And, with COVID-19, we all know that the masks and protective gear are becoming, at least in the short term, a way of life for all of us.
“If you want to stay healthy, you’re going to have to have a mask,” he added. “And, if we can have reusable masks or ensure a supply of masks, that can only make things better for all of us.”
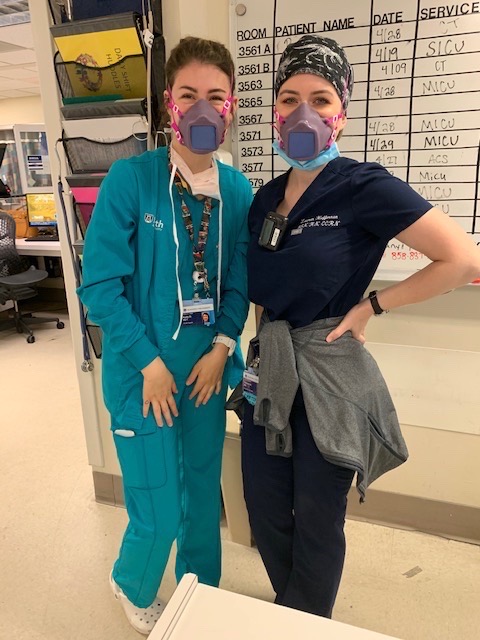
De Greef said Solvay and the other community partners are determined to protect those on the front lines who are battling COVID-19.
“The plan is to continue to print up to 50 molds to develop more masks,” De Greef said. “I can say, we’ve had a good collaboration with Augusta University on this project because we are a bunch of guys who like to help out when we can. And if our contribution can make a difference, we are very happy about that.
“But the people who really deserve the praise are those who are working in the ICU and in the hospitals fighting to protect us from COVID-19. They are the real heroes.”