Hurricane Helene tore a path of destruction beginning at Florida’s Big Bend region and stretching up through Georgia, South Carolina, North Carolina, Tennessee and Virginia. As those affected have slowly been able to grasp the scope, a different form of trouble in the aftermath is creating a ripple effect that will be felt around the region, country and even the world.
Western North Carolina is at the heart of the problem leading to sourcing, transportation and disruption issues. While still trying to understand the full scope of the impact in the most remote areas, ongoing recovery efforts continue following the storm where the death toll has risen to over 250 as of Oct. 14.
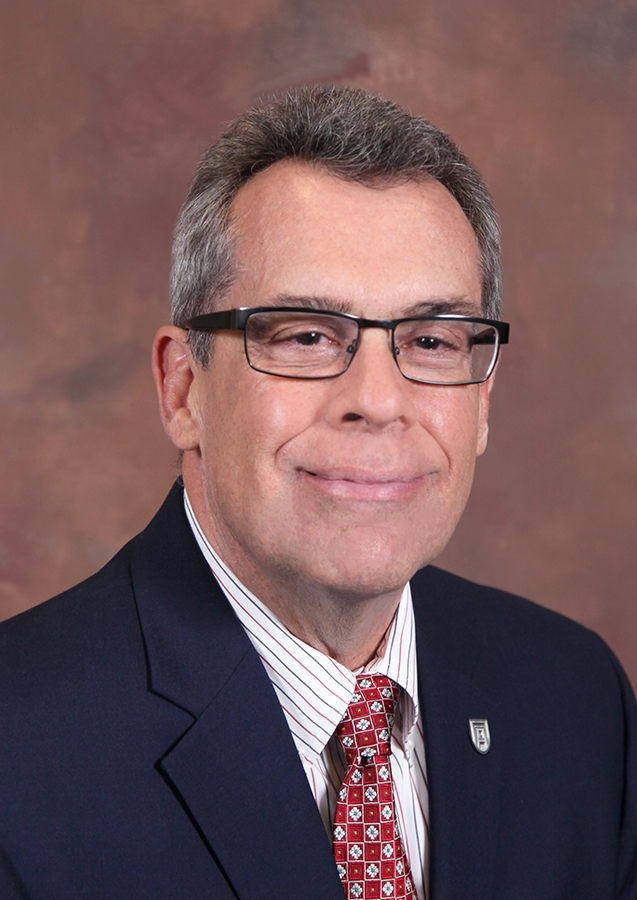
According to Rick Franza, PhD, professor in the James M. Hull College of Business and an expert on operations and supply chain management, said lessons learned from the COVID-19 pandemic and the collapse of the Francis Scott Key Bridge at the Port of Baltimore incident earlier this year can help with mitigation of risk and recovering during these problematic times.
“The biggest thing you’re always dealing with in situations like this is uncertainty,” said Franza. “You can’t expect everything. You can’t anticipate everything, but we learned a lot from COVID-19 and then the Baltimore bridge collapse and the supply chain disruptions those caused.”
Franza said North Carolina is a case study in disruption to the supply chain at three different points: the source, manufacturing and transportation.
“When we think about supply chain disruptions, people don’t typically think about it affecting the physical supply, but rather the transportation and logistics,” said Franza. “This one’s a little trickier because you have one industry affected by the supply of raw materials, another affected by the manufacturing of supplies and so many more will be affected by transportation problems.”
Problems in manufacturing
One industry that has been heavily impacted by the storm is the medical field, particularly the manufacturing of IV fluid bags.
Baxter International, one of the largest producers of IV fluid bags in the country, has a manufacturing plant located in Marion, North Carolina. According to the American Hospital Association, the Marion plant produces 1.5 million IV bags per day, which equates to 60% of the country’s supply.
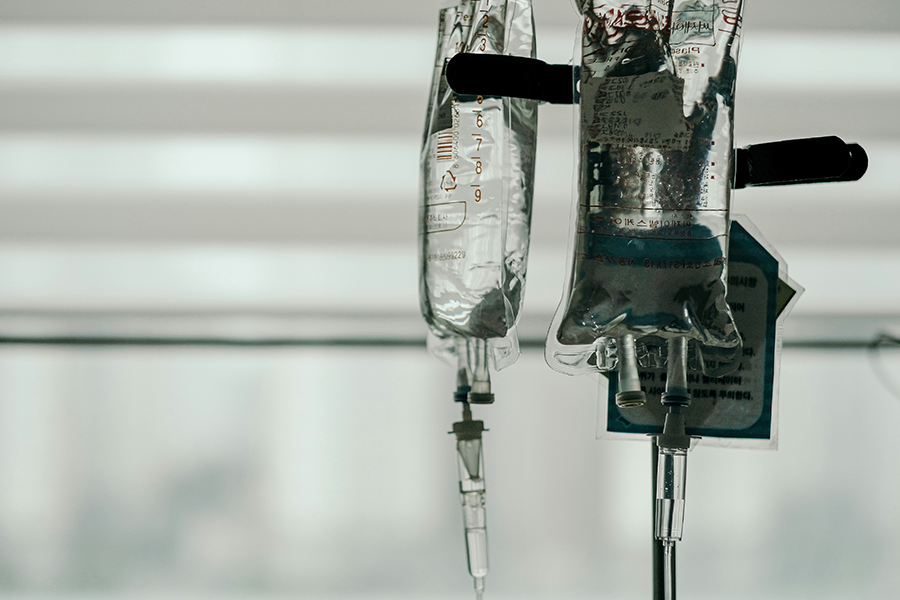
“There are two big questions affecting the supply chain for those IV fluid bags,” said Franza. “If you lose a manufacturing facility, like the one in Marion, does another facility or a competitor have the ability to add capacity, even if it’s just a short term? The other piece of it is, even if they have the capacity, do they have the raw material inputs? So it’s a ripple effect.”
In the wake of the storm, Baxter announced its other manufacturing facilities would increase their capacity. Thanks to its new Mount Carmel Mega Distribution Center located in Mississippi, the company feels confident it will be able to meet the needs of hospitals across the country. Baxter plans to increase allocation levels for direct customers from 40% to 60% and for distributors from 10% to 60%. They are also increasing allocations for designated children’s hospitals by 100%.
Problems at the source
Just outside the town of Spruce Pine, a town of less than 2,200 people located in the Blue Ridge Mountains, are two mines that produce an estimated 80% to 90% of the world’s most pure quartz. The quartz found in those mines is used in the manufacturing of semiconductors for microchips for everything from smartphones to cars to medical devices and more.
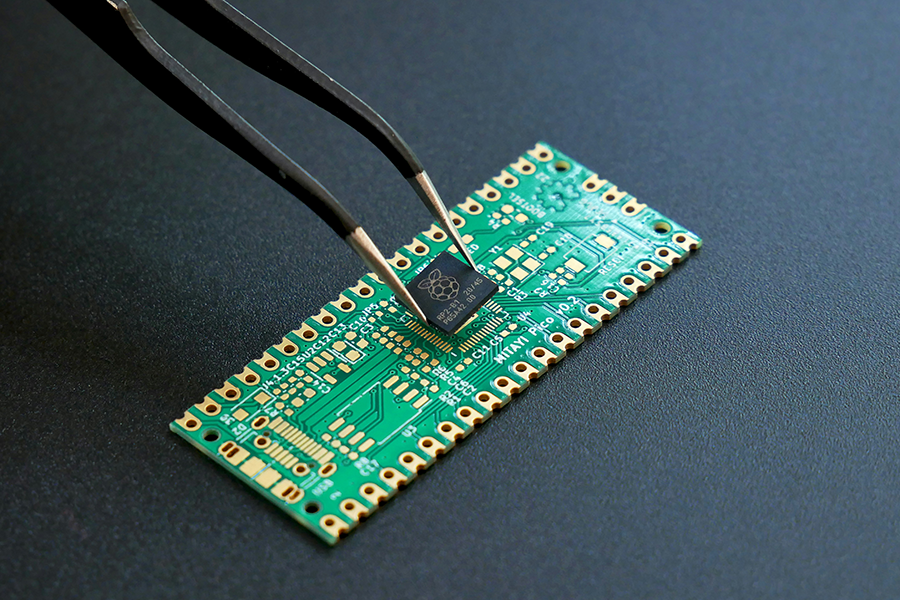
The two companies that manage those two mines, Sibelco and The Quartz Corp, shut down operations on Sept. 26 ahead of the storm. As recovery efforts continue in the region, there remains more uncertainty as the full scope of the damage continues to be realized, and there is no certain timeline for when things will get started again.
“The issue with natural resources like quartz is, unless you’ve come up with some method of producing an artificial version of it, you can’t really make it somewhere else,” said Franza. “Since there isn’t currently an alternative, it then becomes a question of is the mine accessible or how long until it is accessible and people can get back to regular operations?”
Problems with transportation
In Western North Carolina, entire roads along with buildings and other structures were wiped out as streams and rivers surged and mudslides occurred.
On top of getting the mine back up and running, there is also the problem of getting the raw quartz where it needs to go.
“Once you are able to access the ability of the mine to get back online, you then have the problem of whether the raw material can get where it needs to go to be processed,” said Franza. “A big problem in western North Carolina is entire roads are gone, and it’s not a simple repave. On top of that, Interstate 40 is estimated to be shut down until sometime next year, so transportation in that area is going to be extremely difficult for quite a while.”
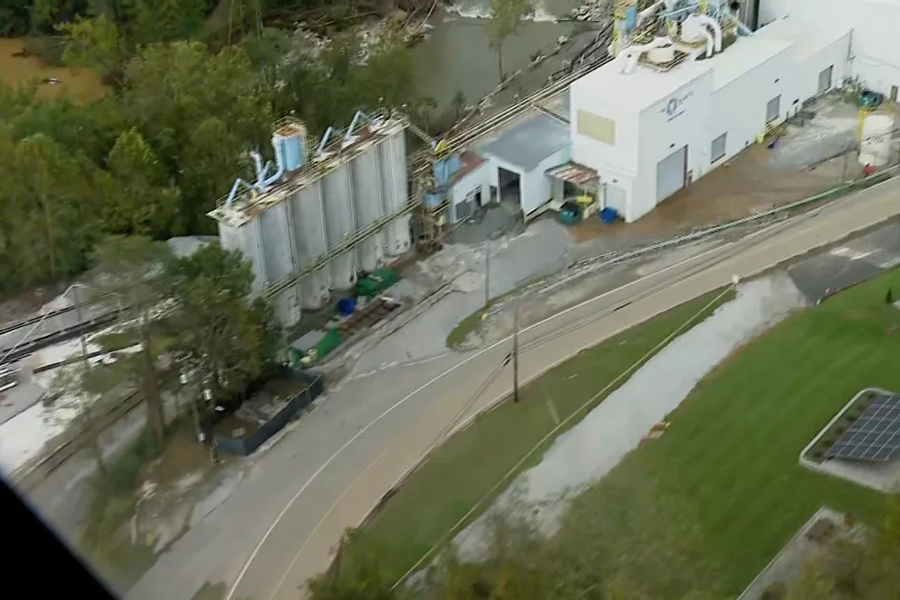
The good news is that quartz and the microchips that it is used in are not perishable items, and some chip manufacturers may have several weeks’ worth of quartz supply built up to be able to continue production. But an extended shutdown will likely mean even more chip shortages, similar to the global chip shortage that began in 2020 and lasted through 2023 due to the COVID-19 pandemic and the tightened restrictions in the countries that manufacture those chips.
The loss of roads is not the only source of recent transportation problems, as immediately following the during the storm there was a three-day disruption in imports at 36 ports, including shutting 14 down stretching from Maine to Texas, as 45,000 dockworkers went on strike over pay.
While that disruption could have caused serious issues, particularly for the upcoming holiday season, Franza said many companies have learned from previous disruptions, and most of the goods needed for Cyber Monday, Black Friday and preparing for the holiday season were already in the country.
“I have heard that somewhere between 80% to 90% of the items for the holidays are already here, so the dock workers’ strike would not have been as much of an issue for the holidays, but there would definitely have been things you’d run out of.”
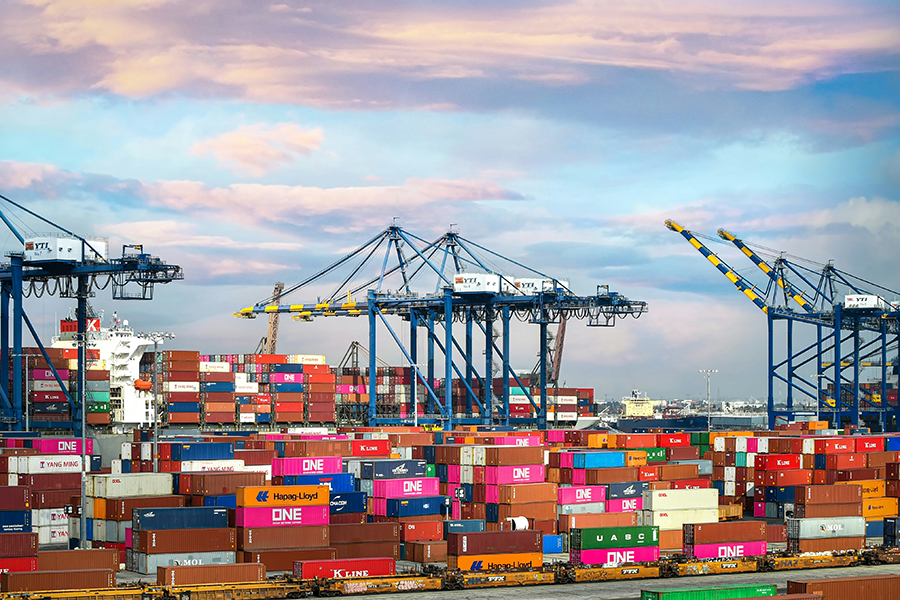
Franza said the biggest problem during situations such as this is misinformation.
“One of the biggest problems is most people are uninformed,” Franza said. “Look at the toilet paper shortage at the beginning of COVID-19. If all of a sudden people rush to buy everything up and hoard it all, you can’t meet that demand so it causes even more problems. People need to be better informed because rumors start and then more problems are caused.”
But Franza reiterated that companies have learned from past events, and that planning has made the supply chain stronger.
“I think we’re better than we were four years ago because each of these crises builds our toolbox on how to plan for and deal with disruptions. It has built resiliency.”